Inside the ‘space factory’
Decades of experience simulating cosmic conditions help Raytheon develop next-generation kill vehicles
It is a place of obsessive cleanliness.
Powerful air filters kick on every 27 seconds, pulling particles of dust from the air with a steady hum. Workers wear head-to-toe “clean room” suits so nothing on their body contaminates the environment – not even an errant strand of hair.
The measures taken every day at Raytheon’s Space Systems Operations facility in Tucson, Arizona, make sense when you consider the magnitude of the work that happens there. Inside the 49,000 square-foot facility, a team of technicians, engineers and operators develop, test and assemble parts for highly precise defensive weapons known as “kill vehicles” that track and defeat ballistic missiles in the vacuum of space – an environment the site was designed specifically to recreate.
Recreating space
Raytheon’s “space factory” is a controlled environment where the business works on interceptors to track and defeat ballistic missiles. Those interceptors include:
The SM-3 interceptor, which destroys short- to intermediate-range ballistic missiles and whose latest variant can launch from land and sea
“Years of rigorous engineering, rigorous cleanliness and rigorous testing ensures our defenses will work reliably when faced with a real threat,” said Justin Jenia, vice president of Strike Initiatives at Raytheon, an RTX business.
“We have 25 years of iterative experience and data from 50 successful space intercepts,” Jenia added. “What we learned, what we saw in these increasingly complex test scenarios has led to significant efficiencies and process improvements in our factory assembly and environmental controls.”
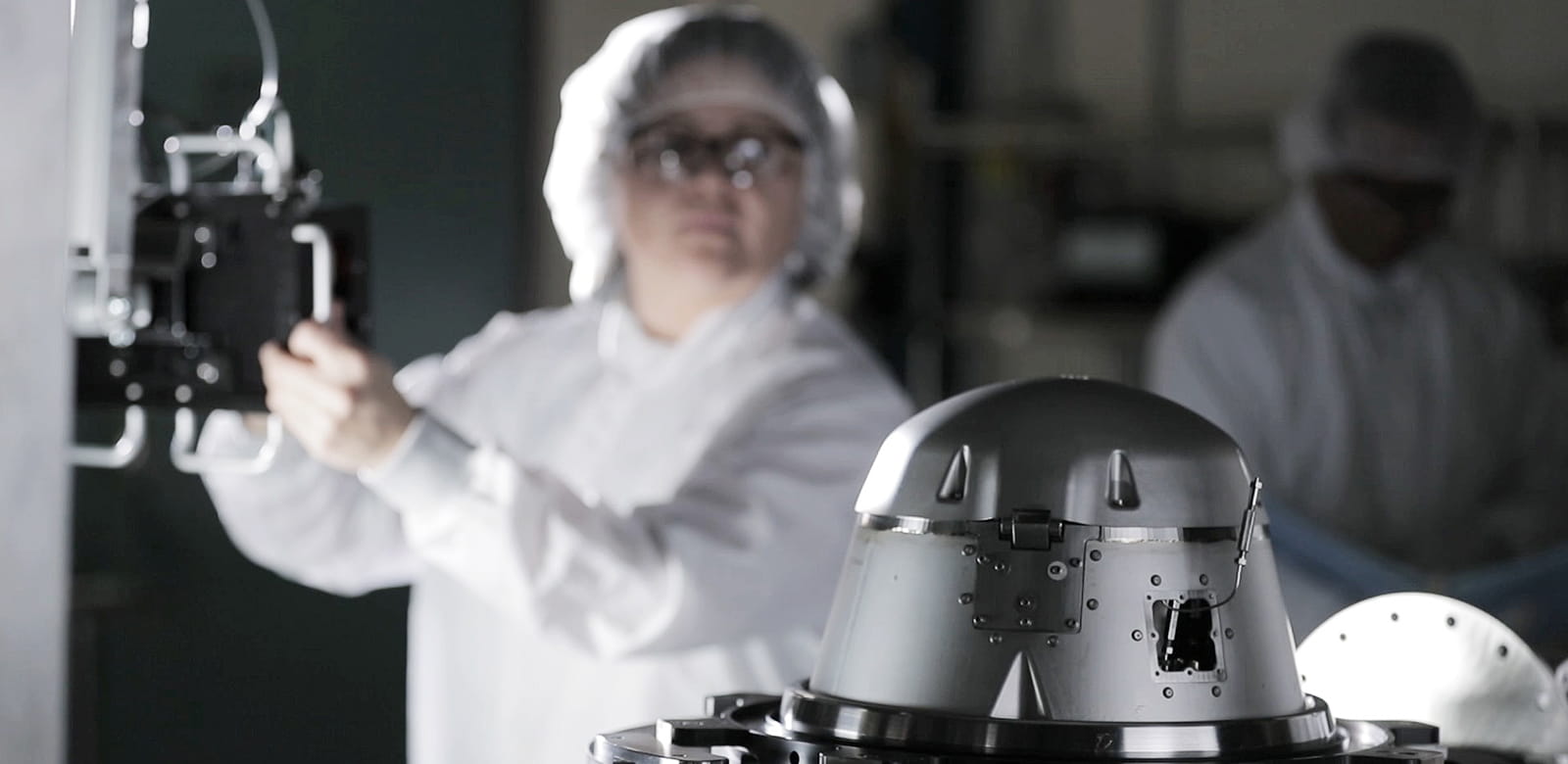
At the space factory, air is filtered out every 27 seconds to simulate the exoatmosphere, where even a miniscule fleck of dust can damage instruments and systems.
Why so clean?
Keeping an exceptionally sterile environment is important when working with precision optics and sensors. And it’s even more important when those optics and sensors are going into such a high-stakes situation.
“Any tiny particulate on the lens will look like a target-like object and affect the probability of intercepting the actual target,” Jenia said. “Keeping the vehicle impeccably clean throughout assembly, testing and shipping to the ground-based launcher is hypercritical.”
Stainless steel is the metal of choice in the space factory for particle mitigation, while sensors throughout the building constantly measure air pressure, temperature, humidity and microscopic particles.
The facility is the birthplace of the EKV, which marked its 13th intercept during a test in December 2023 run by the U.S. Missile Defense Agency and U.S. Northern Command. The weapon slammed into and destroyed its target, a mock intermediate-range ballistic missile, over the Pacific Ocean.
The latest successful test came as a triumph but not as a surprise; it reflected the findings of thousands of virtual tests conducted through modeling and simulation technology, in addition to tests of the physical hardware.
“Early on, our models were good, but far from perfect because we had no data to anchor them to like we do today,” Jenia said. “We have 25 years of data from real test events and intercepts that we can drive back into our models to mature their accuracy.”
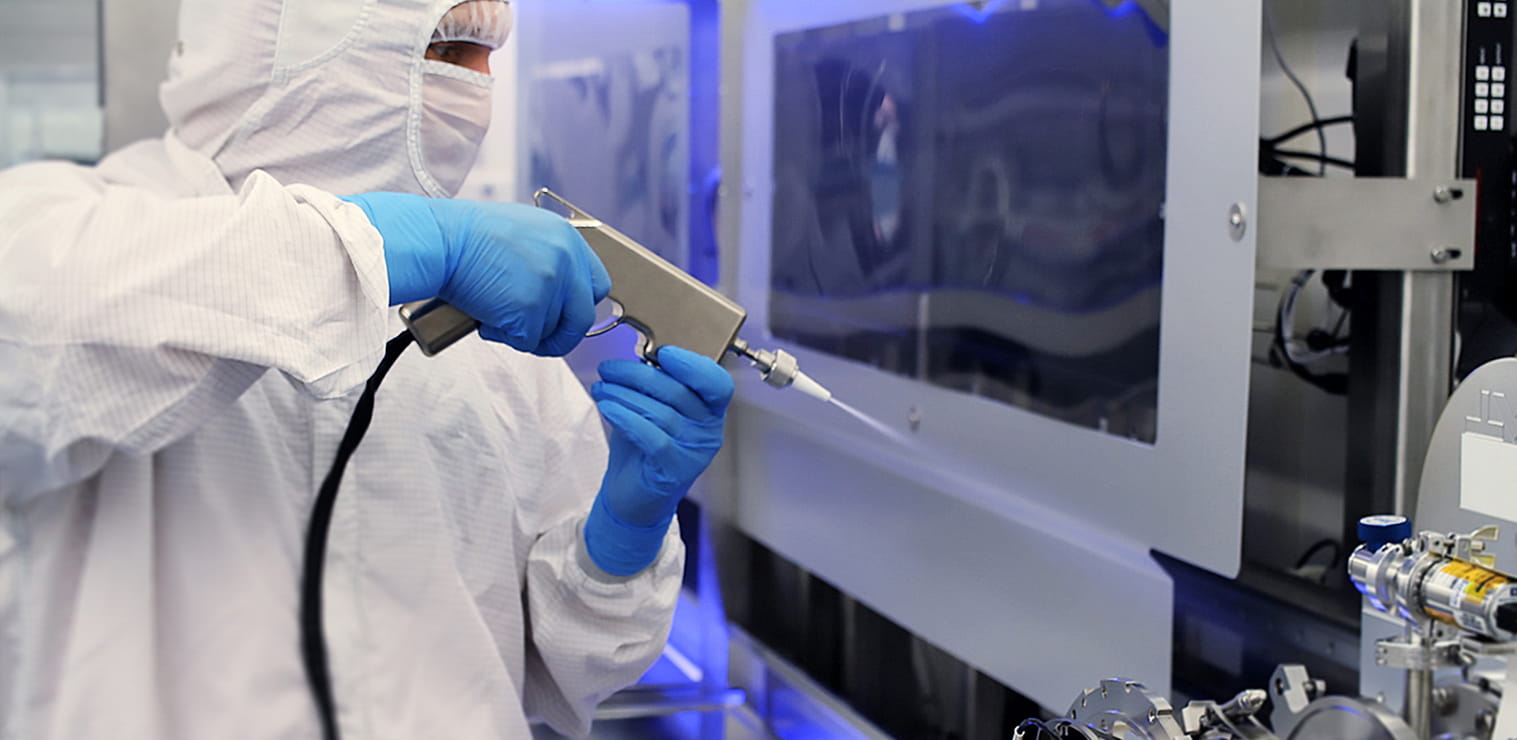
At the space factory in Tucson, a technician tests exoatmospheric technology in an ultra-clean environment.
Dedicated to the mission
Jenia, who joined Raytheon more than 20 years ago as the business and the U.S. Missile Defense Agency were ramping up their mission, has seen the systems now being tested and deployed in their earliest stages.
“As a young engineering intern turned full-time employee, it was quite an adrenaline rush to apply what I learned in school to real-world situations,” Jenia said. “It was about this exciting, exquisite, high-end, high-tech engineering when I was young.”
He recalled a pivotal career moment when the government-industry team achieved their first intercept in 1999.
As he recalls it, after all the high-fives and cheers, a member of the military delegation stood up and said, “Congratulations, we just demonstrated something that someday potentially will save Los Angeles or Washington, D.C.”
“It’s a memory I’ll never forget. I was already on this high that our engineering and our team’s efforts came to fruition,” Jenia said. “It really drove so much passion and excitement into me so early in my career.”
All views are those of Raytheon and do not imply endorsement by the Missile Defense Agency.
Space factory highlights
Since expanding the facility in 2015, Raytheon has invested in its capabilities. Among the updates:
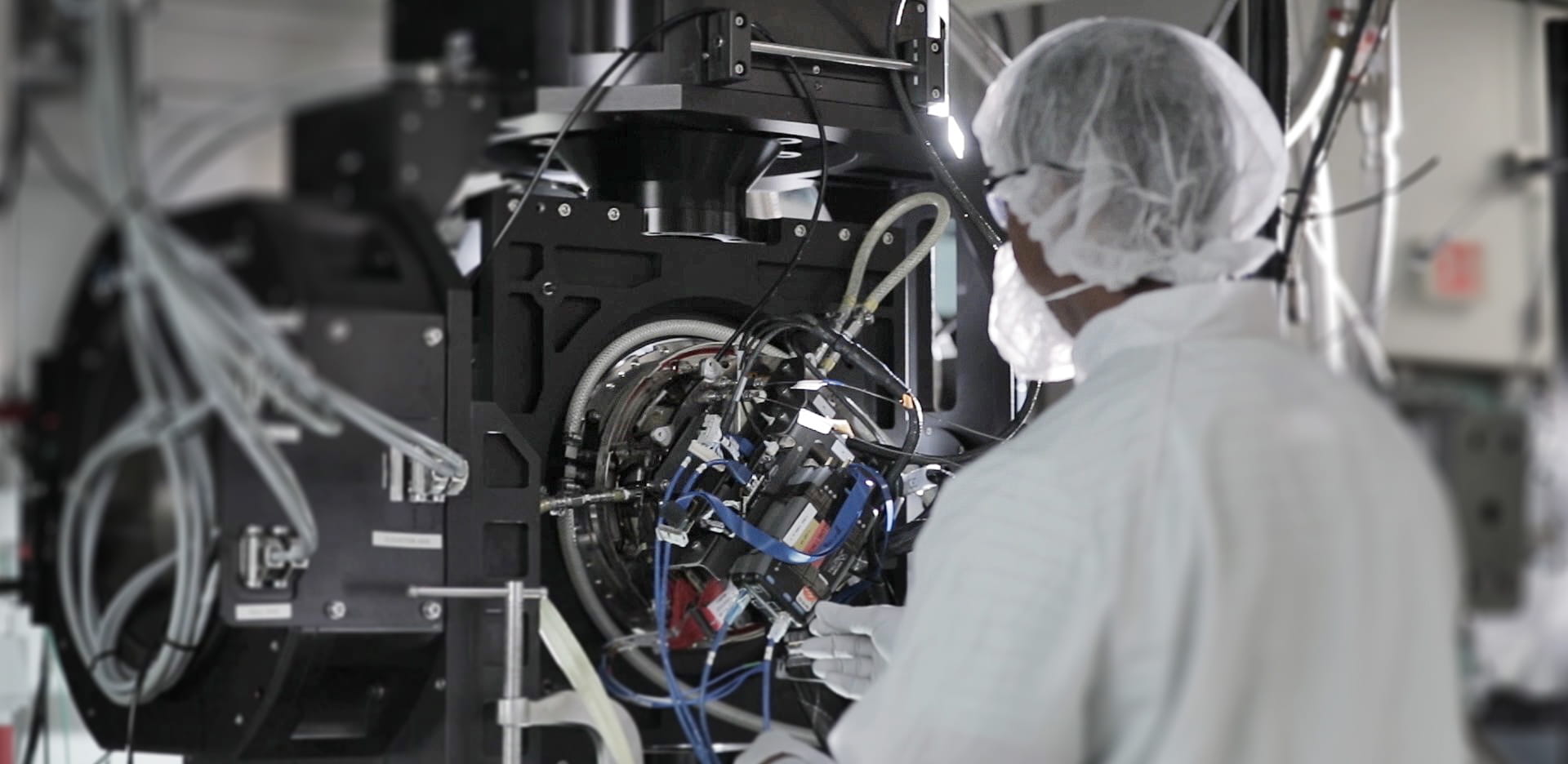
Technicians and engineers support production and testing of complex space hardware at the space factory, where sensors constantly ensure its air pressure, temperature, humidity and microscopic particles continue to simulate space.