EAGLE Logistics Toolset
For over two decades the Raytheon EAGLE team has been developing world-class software solutions designed to support the production and management of program logistics, technical manual development, and product support data. All of the products listed below share a centralized database which means that there is no need to create complex interfaces for moving GIEA-STD 0007 Task data from your Logistics Product Database into your S1000D or 40051 compliant technical publications. Provisioning data developed in your Logistics Product Database can be used to baseline your parts inventory and As-Built configurations in your Maintenance Management System.
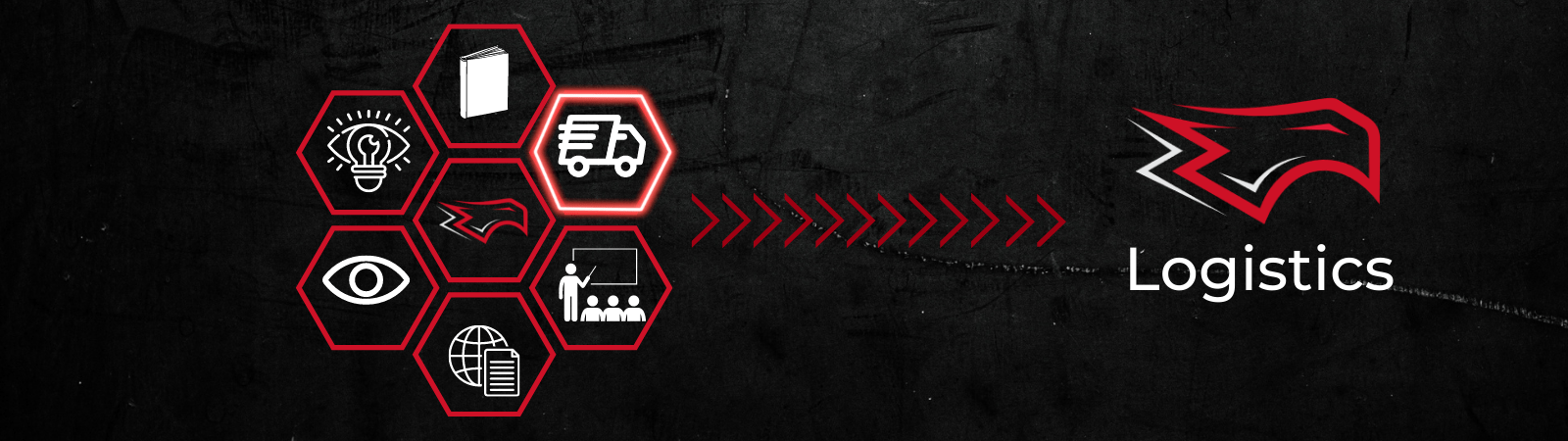
The EAGLE Logistics Product Data, or LPD, tool is a logistics system using a central database repository for the development of fully compliant logistics products for a variety of military specifications, including GEIA-STD-0007 (Rev A & B), MIL-STD-1388-2B, and DEF STAN 00-60 (all Issues) with DEF(AUST)5692 on the horizon.
EAGLE utilizes an indentured parts list/bill of material loader to generate a spec-compliant breakdown and can backfill LSA data as well as an ad hoc table interface for bulk loading and editing. A featured interface allows for tailoring information by way of cloning, referencing, or adding & editing records individually by functional area. Entire branches can be moved in a breakdown view of the project and entire breakdowns can be mapped to particular variants in a matrix view of the complete system.
EAGLE automatically builds all standardize logistics reports, exchange files, and integrates with the EAGLE Publishing System, or EPS, to flow LSA data into technical publications on a single database instance which meet the requirements of ASD S1000D and MIL-STD-40051.
Features
EAGLE Ad Hoc is a powerful reporting tool that allows users to easily create simple or complex SQL-based reports that can be tailored to extract data from EAGLE, EPS or MMIS. After an Ad Hoc query is executed, data can be updated on the fly, and new rows can be imported by cutting and pasting directly from Microsoft Excel. This feature allows you to cut and paste 1000s of rows into the database with a couple of clicks. Ad Hoc queries can also be stored in the database for future use.
Creating your initial LCN structure can be complicated and time consuming, particularly if you are new to the concept of LCNs. The EAGLE Bill of Materials importer allows EAGLE users to easily transform indentured parts lists from Microsoft Excel into GEIA-STD-0007 or other LPD formats. Users can specify the LCN structure, format, and gaps, then preview what the LCN breakdown structure will look like before updating the EAGLE LDP database. Users can also select what LDP tables and columns to backfill, and are provided with a report that highlights any potential data quality issues so that they can be corrected.
If you have a new LPD requirement, and an indentured parts list, the EAGLE BOM importer is the way to go.
EAGLE Breakdown Navigation is an intuitive tree-based application that gives users the ability to visualize a functional or physical product breakdown structure of the end items and systems that reside in the EAGLE LPD repository. Output can be viewed as an LCN breakdown, or Part Number breakdown and can also be filtered by Usable On Code (UOC). This feature is a must for programs that have several product variants. From the EAGLE Breakdown navigator, users can easily jump from any item in the tree to Provisioning, RAM, Task Analysis, Transportation, as well as documents and drawings.
EAGLE Task Analysis gives users the ability to easily create and update all LPD-related task data in one module. Users can enter new task codes, add task frequencies, support equipment, provisioned items, mean man hours, annual operating requirements, facilities requirements, training requirements, subtask data, subtask narrative, work area codes, personnel, and much more.
Additionally, if your program has LPD and S1000D or MIL-STD-40051 requirements, task data entered into the EAGLE system can be transformed into work pages or data modules with the click of a button. This feature allows for tremendous savings and excellent data quality and consistency because the task data developed for your LPD will now match your Tech Manuals.
The EAGLE Reliability and Maintainability module allows users to manage all system reliability LPD information in one centralized system. Users can enter RAM data such as wear out life, logistics considerations, failure rates, maintenance and support concepts, item function information, system accessibility and training considerations, and mean time between failure information.
Additional product attributes such as failure and damage mode indicators and failure mode ratios can be documented and Reliability Centered Maintenance results can be performed and stored in the database for use in maintenance task analysis related activities.
After RCM analysis is performed, failure modes can be linked with maintenance tasks, along with maintenance intervals, task types, and measurement bases for use in Task Frequency and Maintenance Repair rate calculations.
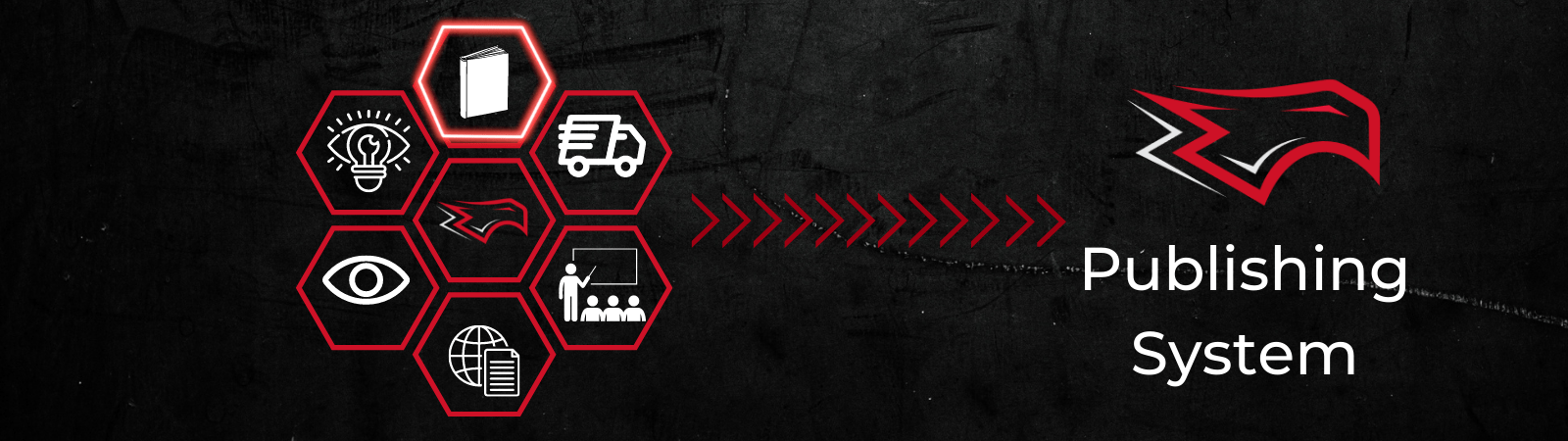
Robust and intuitive software for the authoring and management of electronic technical manuals.
The EAGLE Publishing System is a CSDB that allows users to manage their technical publications in a standardized format (XML and SGML). The EPS allows the users to author and manage their technical content utilizing built in workflow and configuration management with an integrated XML editor included with the software.
EPS was designed by the Raytheon EAGLE team from the ground up to be fast, powerful, intuitive and robust. It incorporates many user requested features to facilitate rapid data production and includes program management functions that facilitate on-time production at minimal cost. Easy-to-use productivity tools and features assist the technical writers to produce and validate content quickly and accurately.
Features
EPS includes a fully integrated SGML/XML editor with real-time what-you-see-is-what-you-get content view and navigation. The editor has the ability to search the database and assist the author to create references to internal and external objects, and it continuously checks the content for schema validity and conformance with the business rules, helping technical authors produce data quickly and accurately.
Utilizing LSA data in a technical publication is seamless with the EPS and the EAGLE LPD tool. This allows the existing data to be re-used and remain in sync with the technical publication. Engineering changes can be immediately incorporated into a publication using our "Build from EAGLE" tool.
Included is a very powerful publishing engine which allows publications to be output in PDF or IETM format. The tailorable stylesheets allow for customized output to fulfill the demands of the customer.
The EPS supports S1000D, MIL-STD-40051 and MIL-STD-3001 as well as other specs such as the JSF 2.1 and the FSAF 3.0 specification. Our world-renowned EAGLE support will ensure that the latest version of each specification will be supported.
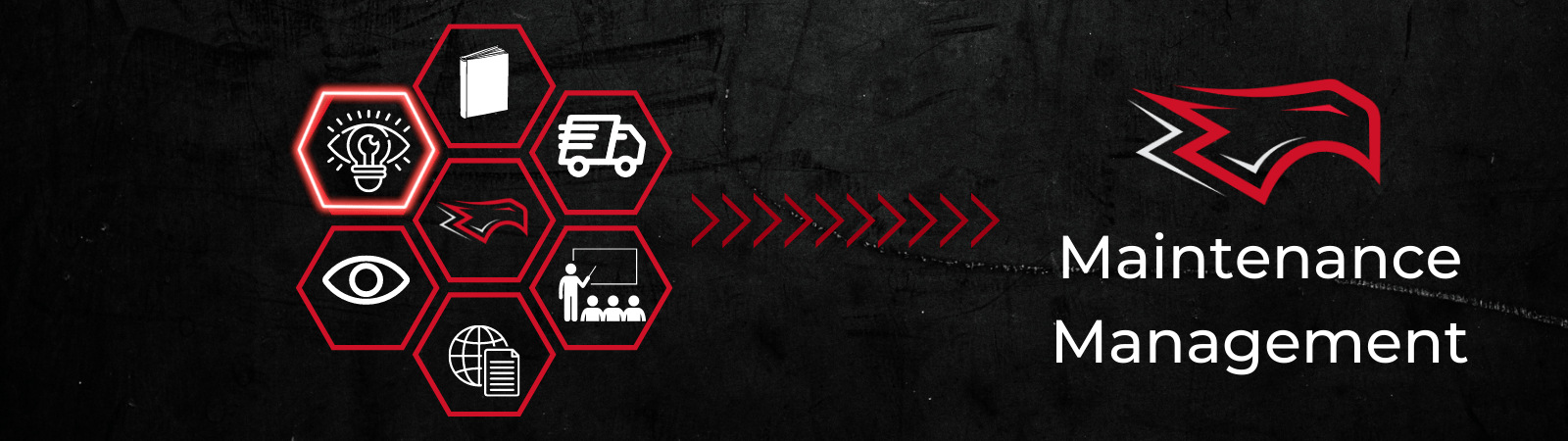
At Raytheon, inventory management extends beyond simple inventory tracking. Continuous improvement is engrained in our culture, and we have set up several standard practices that infuse inventory management with other disciplines such integrated logistics support analysis, reliability engineering, and configuration management. We understand that the product life of a weapon system can span decades and monitoring reliability trends and diminishing suppliers is critical if we are going to exceed the operational requirements of our customers. Raytheon has developed a software system that unifies FRACAS, configuration management, preventive maintenance and inventory management - the EAGLE Maintenance Management Information System.
With MMIS, inventory items can be serialized or un-serialized and the configuration of these items can be tracked over time via our MMIS AsMaintained Configuration module. Special care is taken to ensure that CAGE Codes, Part Numbers and National Stock Numbers are controlled and approved by the proper engineering authority. If the contractor chooses, these part numbers can be tracked in MIL-STD-1388-2B or GEIA-STD-0007 repositories to ensure conformance to standard logistics support analysis practices. Software and firmware configuration can be tracked and parts can be categories and consumables, test equipment, repairable, and long lead items.
Features
Inventory can be tracked geographically to the site/location/shelf and bin level and every material movement transaction is recorded for audit purposes. Inventory condition and value can also be recorded. Barcoded items can be registered in the MMIS inventory system and IUID labels can be created in various formats. As material is shipped between sites and locations, shipping and receiving documents can be created for audit purposes and applicable shipping documents such as DD1949s or DD1348s can be created.
Inventory criticality and lead time can be stored and if required, economic order quantity analysis can be performed for each inventoried item. Reorder points and minimum stock levels can be monitored, and rolling-through-time calculations can be performed if demand metrics are available. Failure rates and mean time between failure data can also be associated to each inventoried item.
Scheduled (PMCS) and unscheduled maintenance can be strategically planned and executed using the MMIS Workflow system. Preventive maintenance schedules can be created and applied to applicable inventory based on various triggers such as calendar days, operation hours, or other customizable measurement bases. Maintenance performed by field service representatives can be monitored and requests for spare parts can be easily dispatched.
Standard workflow operations (or routes) can be assigned to parts that enter the depot for repair. Condition code and status can be recorded for each WIP item and metrics such as Repair Turn-Around Time, Operational Availability, and Mean Time Between Failures can be calculated. Standard performance metrics such as touch labor estimates can be recorded and compared with actual labor hours and applicable support equipment, required conditions and consumables can be attached to each maintenance task that is performed. Work instructions can be created and attached to operations in MMIS for reference. Documentation such as shipping and receiving forms, maintenance actions forms, certificates of conformance, and failure data can be attached to each work order for future reference.
Every remove and replace procedure can be logged for future reference. Defective component and root cause analysis can be performed on repaired items as they move through the depot. This information can be synthesized use by reliability engineers for FRACAS reporting. If defect trends are identified engineering changes, training requirements or process changes can be presented to all stakeholders via a Failure Review Board or similar processes. If engineering change orders are created, MMIS can manage the incorporation of those changes.
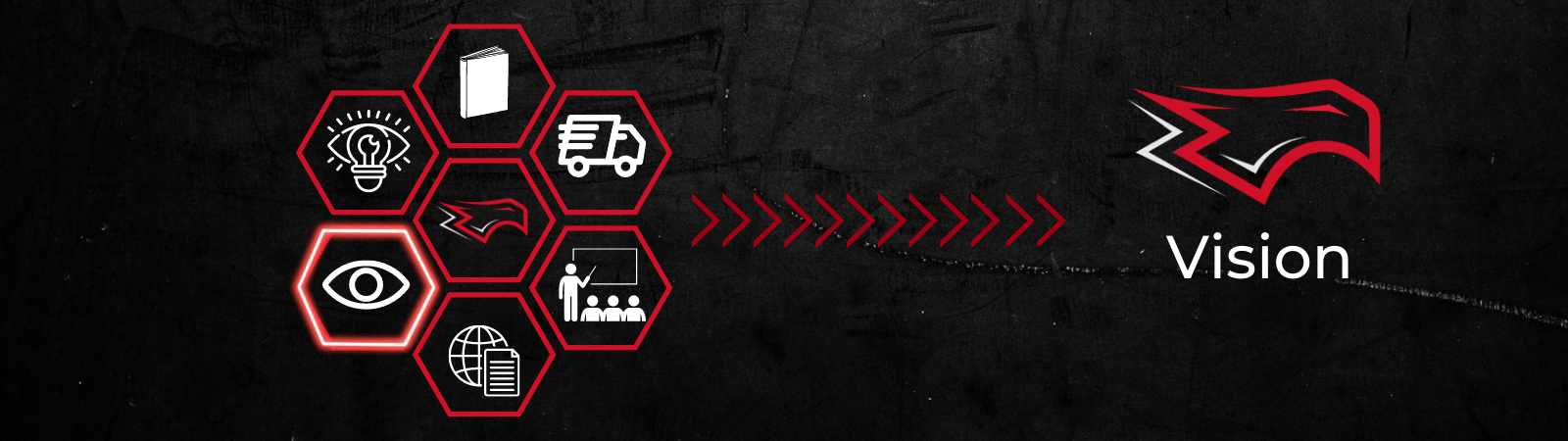
EAGLE Vision is an IETM viewer, similar to the EPS Previewer, which is able to display hyperlinks to other objects such as paragraphs, steps, graphics, tables or even other data module content. However, unlike the EPS Previewer, EAGLE Vision has been created as a web-based application to be more portable, now you will no longer need to have EPS installed to view publications. Once EAGLE Vision is set up on a web server and linked with the licensed builder, you will be able to use any laptop, tablet or smartphone, with access to the remote server, to view IETMs that have been deployed by the builder application.
This viewer has been developed to support any data module type currently supported by the EPS Previewer. This means that graphic formats such as CGM and SVG are supported without any third-party plugins. Linking and viewing hotspots are also supported with the EAGLE Vision graphics viewer.
EAGLE vision allows IETMs to be downloaded for offline viewing.
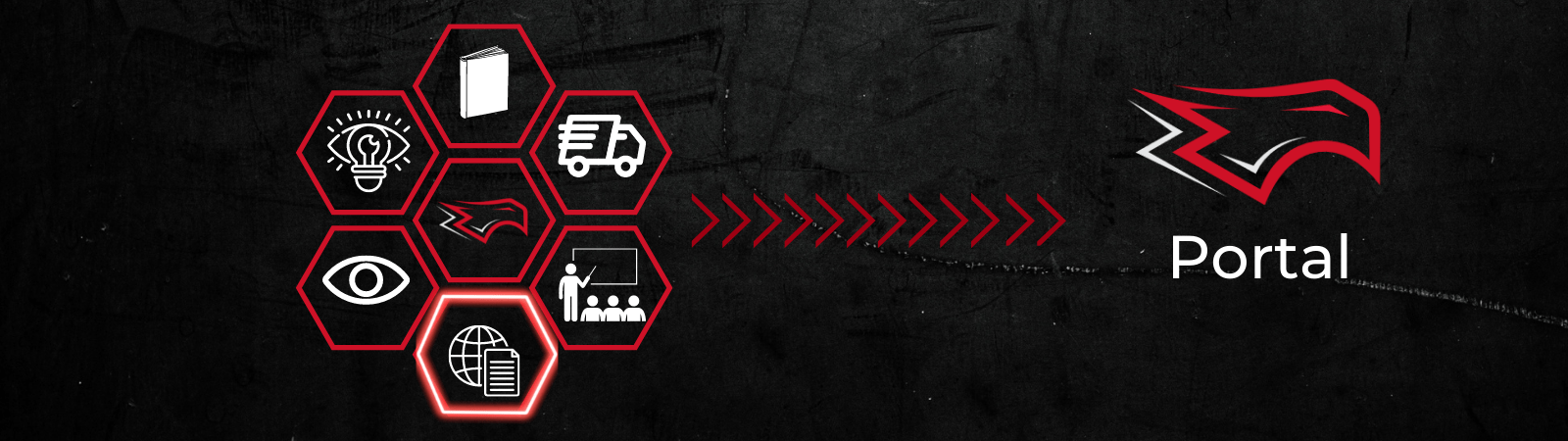
The EAGLE EPS Web Portal is a web application that gives customers and end users a quick and easy way to review S1000D data modules, publication modules, as well as entities. This greatly reduces the amount of time it takes for the review process by giving specific users access to view the data and publication modules.
Users with access to a project will have the ability to view the associated data and publication modules in both PDF and Interactive Electronic Technical Manual format. They will be able to locate specific data modules and publication modules by using the Finder Filters, which will help narrow down any search results. Users will also be able to post comments on each data or publication module, as well as upload any additional attachments.
Uploaded attachments can range from Microsoft Word documents and images to annotated PDFs. The author will be able to see these uploaded attachments instantly, and can proceed with any changes suggested by the reviewers.
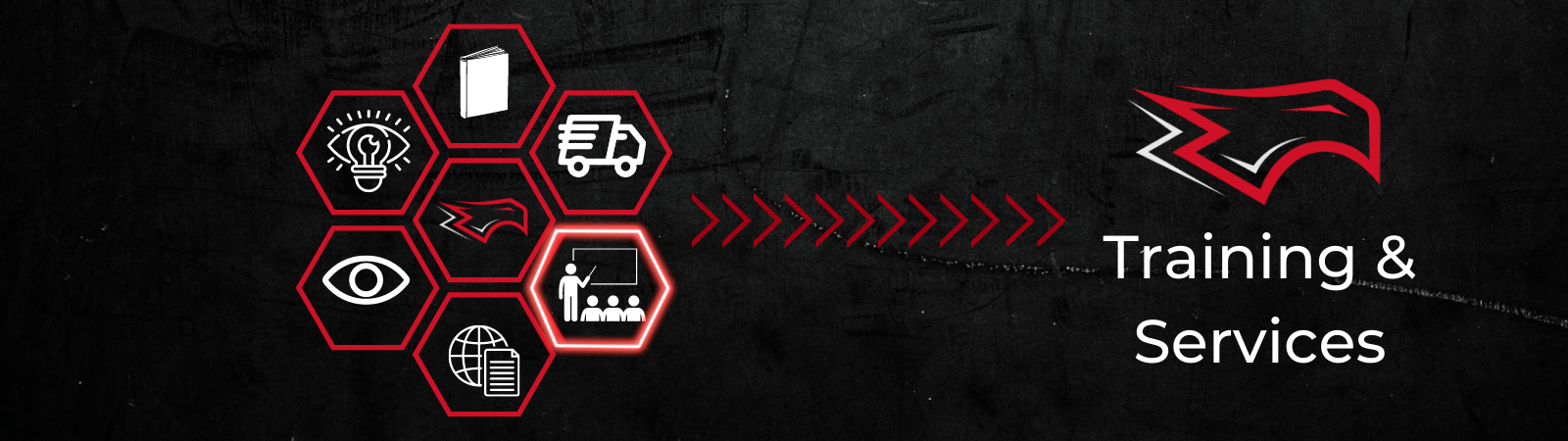
Introduction to the EAGLE Logistics Product Data
This course introduces students to the Enhanced Automated Graphical Logistics Environment Logistic Product Data solution. It includes the fundamentals of Integrated Logistics Support and Logistic Support Analysis. The EAGLE client is used in a workshop setting to develop logistics data and produce sample output reports and files. The training can focus on the logistics product data standard of choice; MIL-STD-1388-2B, DEF STAN 00-60 or GEIA-STD-0007.
Introduction to EAGLE Publishing System
This course instructs students in how to use the EAGLE Publishing System to create valid technical data. The training can focus on the technical data standard of choice ASD S1000D or MIL-STD-40051-1. The topics included in the core training are: ASD S1000D, structured XML authoring, creating projects, creating and validating data, workflow and roles, exporting data and publishing. If required, the training can include exercises in the use of EAGLE LSAR data to automatically generate procedural and Illustrated Parts Data Modules. The course concludes with a high-intensity collaborative workshop that consolidates the learning and provides a roadmap for production projects.
Follow-on consulting is offered and recommended. Our knowledgeable and experienced instructors can provide detailed advice and assistance to programs to establish production projects. This can give projects a head start and avoid the need re-work data later on.
EAGLE Maintenance Management Information System
The purpose of this training course is to familiarize the student with how the Maintenance Management Information System is used to capture and utilize contractual data requirements in the depot repair process. Topics include Engineering Change Proposals, Lessons Learned, AsBuilt/AsMaintained Configuration Management, Inventory Management, Contracts, Document Management, Failure Reporting and Corrective Action, and Traveler/Workflow Management. These are all common functions in both Contract Logistics Support and Performance-Based Logistics contracts used in the aerospace and defense industry and are vital components in process improvement, quality, and superior system readiness. This course also provides an overview on how the Logistics Support Analysis Control Number is used in EAGLE to model a hierarchical parts breakdown and how that breakdown is used in MMIS in the context of FRACAS and AsBuilt configuration management.
In addition to the core training courses offered, the Raytheon EAGLE team is comprised of software developers, specialists and engineers who have many years of experience on a bewildering range of programs.
If you have a need for a tailored or advanced class or perhaps want to take advantage of expert consulting services to save time, effort and costs in getting a project off the ground, we are in a position to offer this on request.
Typically training events are held in person at the customer site using the EAGLE database and client applications owned by the customer.
Students are also invited to attend training events in the EAGLE training facilities in Tucson, Arizona or Huntsville, Alabama.
From our experience, our maximum class size is restricted to a maximum of 10 students.
Classes are scheduled to last a working week.
We also provide other services to assist you with your success, such as Custom Engineering, System Integration, Hosting, and Network Services. Our engineering team has assisted with legacy data conversions, system administration services, and tailored product support solutions.
If you need assistance with technical authoring, Raytheon Intelligence & Space has a broad network of business partners that we can work with to suit your needs.
Questions?
Please reach out to [email protected] or use the link below to request a product demonstration, get pricing information, or ask technical questions. Thank you for your interest in EAGLE!
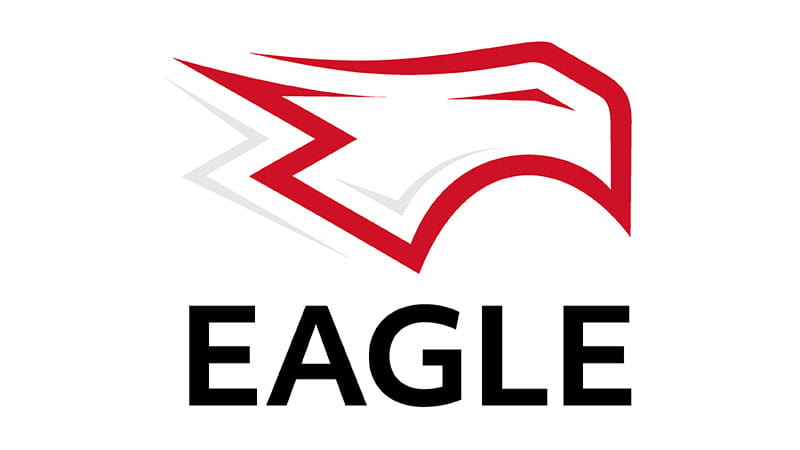